How to SuperSonic:P1 design a super sonic airfoil(如何超声速:P1设计一个超声速翼型)
There was a day I randomly searching online. And I can’t really find it again, but there are two kinds of classical supersonic airfoil which are Biconvex airfoil and Wedge or double wedge airfoil and interestingly Wedge Airfoil actually has lower supersonic drags than Biconvex Airfoil.
Also I kind want a better supersonic airfoil design, so I start this project.
Talking about supersonic the most important thing is wave drag. To minimize wave drag a basic idea is shaping its cross-sectional area close to Sears-Haack body which has minimum wave drag.
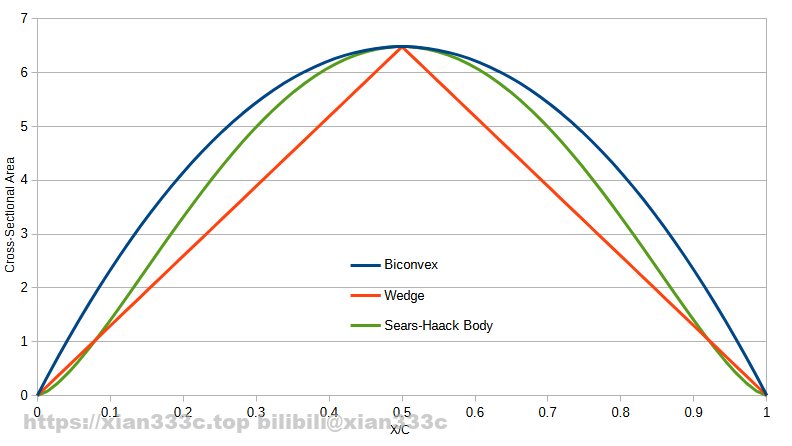
Here is airfoil cross-section of Biconvex and Wedge comparing to Sears-Haack body. You can find that none of it looks shaped well. So here is an airfoil that I designed it to be close to Sears-Haack body and I can scale it to be thickness whatever I need.

It is what it looks like. Also, I gonna leaves Airfoil point file so if you want to try it. I asked AI for any idea of this Airfoil’s name. So this gonna be WaveTrim Foil with thickness following behind.
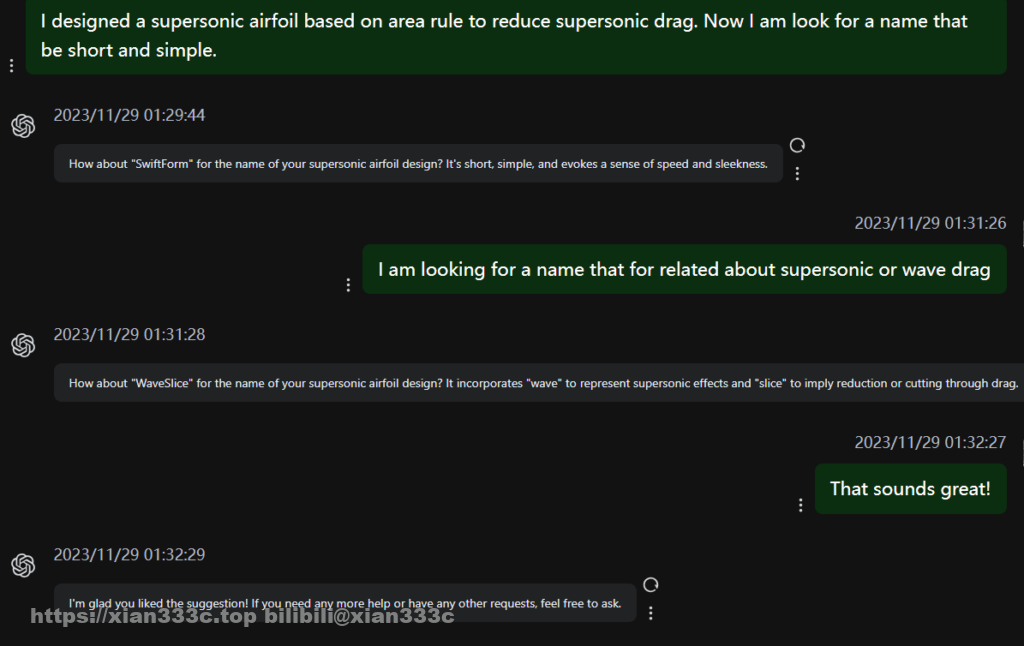
To figure out its performance I ran CFD analysis of these airfoils at Re=2835020 and Mach 1.38. I run it up to 30 degrees angle of attack but in high angle of attack flow separation makes it not steady so it’s not really accurate at high angle of attack.
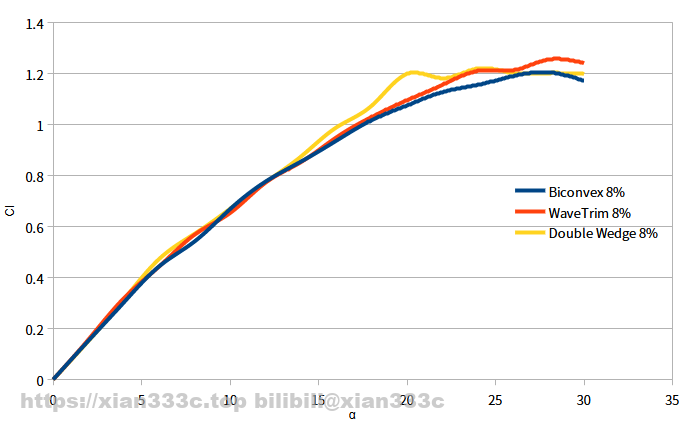
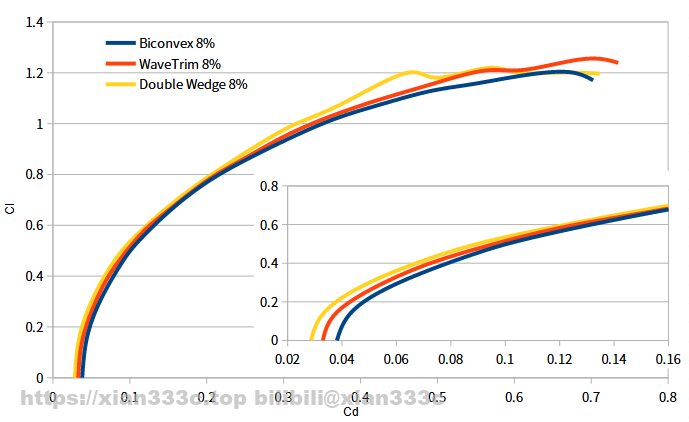
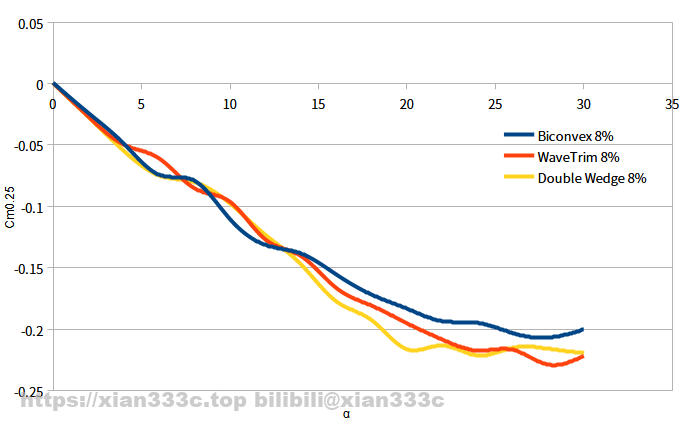
With it alpha-Cl graph didn’t looks very interesting, and Clalpha at supersonic even in this case of 2D airfoil is very low compared to subsonic. Cd-Cl graph what you can find is that Wedge Airfoil is really performing better than Biconvex, even having the lowest drag. My WaveTrim Foil design is somewhere between Biconvex and wedge. And here is pitch movement of 25% chord line and Aerodynamic Center, not very interesting.

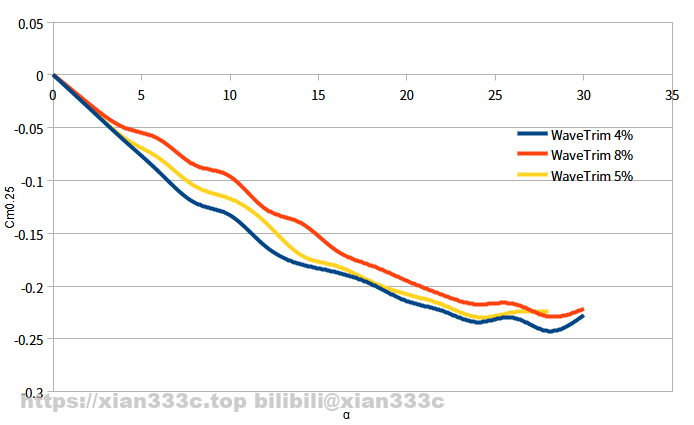
I also CFD analysis with different thickness, clearly you can find that thickness is the most important factor of supersonic drag because thickness directly impacts wave drags. Cd-Cl graph looks like drags of 0 angle of attack are kind like an offset of the curve, and also heavily affect the maximum Lift and Drag Ratio. So in supersonic you always should be trying to make your airfoil as thin as possible.
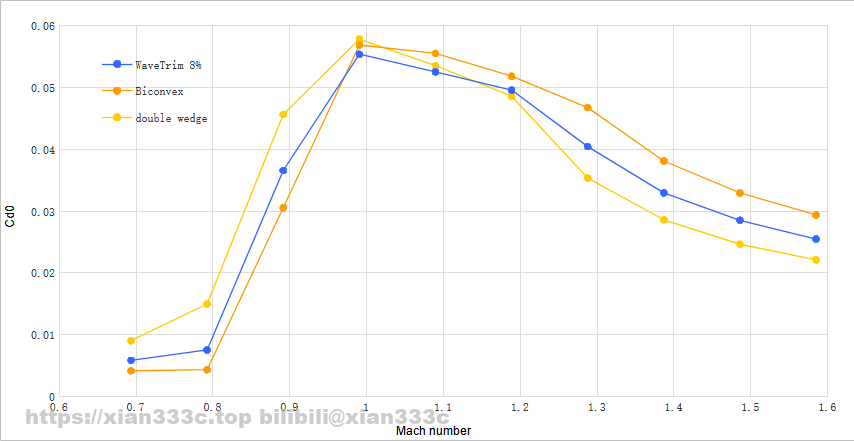
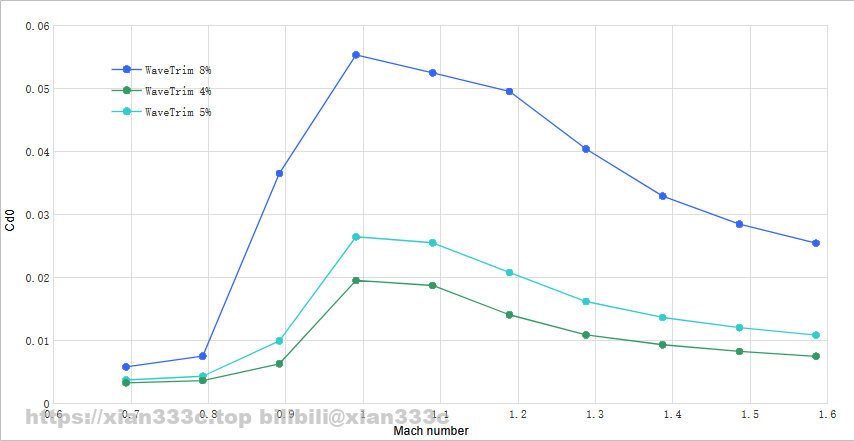
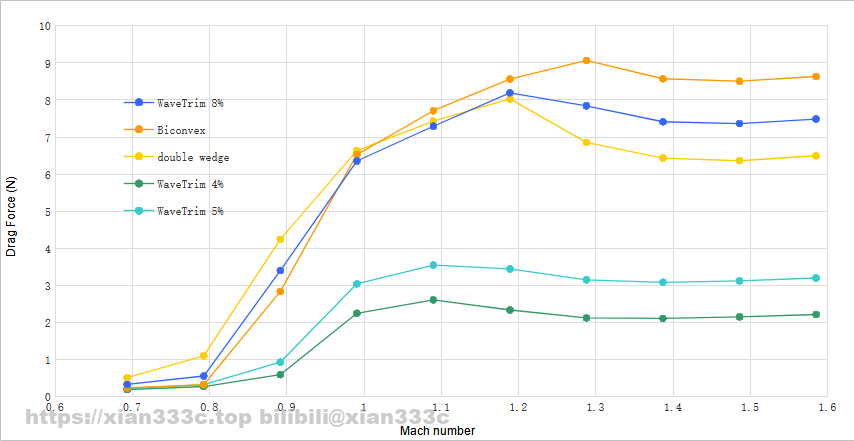
At last I analysis of these airfoil’s zero lift drag from subsonic to supersonic range. Actually, my WaveTrim Foil performs best at trans sonic from ruffly Mach 1 to Mach 1.15, for any higher Mach number Wedge appears to be better, and in subsonic speed Biconvex performs best and Wedge is the worst. Looks like you can’t take both of it, and My WaveTrim Foil is always in the middle.
So that it for this project, I designed a supersonic airfoil that performed quite decent. And there will be a link to download this foil if you need it.
But that doesn’t mean there is nothing left to do. I think it there is still lots of further work I can do, for example WaveTrim foil is just an airfoil that I shaped to reduce wave drag, and it is hard to do more design based on it because there isn’t some kind of way to accurately describe it shape. I am already working at use a function to describe shapes and based on that I can easily extend this design and can able to use some factors to determent a specific shape, just like the NACA series airfoil.